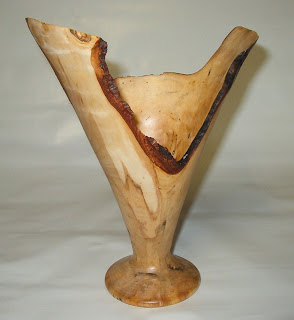
I have been working on some things for the new website in answer to questions specifically from beginners. More and more I am convinced that we need to get back to the fundamentals of turning. In some ways the direction of turning today seems to reflect the direction of education.
Our educational system in North America appears to be ranging away from the fundamentals of societal need to move toward specialization without foundation. By that I mean for example that students are preparing term presentations with video cameras before they can write a script, or for that matter a coherent sentence. Algebra appears to be on the curriculum for students who cannot handle basic arithmetic without a calculator. It used to be that employers considered a high school graduate suitable for training for managerial positions. Now they hope that college graduates can read, write, and balance a check book, but there are no guarantees. Many colleges and universities have entry level courses, mostly non credit, to teach the basic skills of reading, writing and arithmetic to incoming students, some of whom were A level graduates of high schools but lack basic skills.
In the same manner, I hear people having bought lathes to turn salad bowls for a living or baseball bats for the team, but have never used the machine before. Many a would be turner goes to the lathe for the first time, puts on a length of construction 4x4, and watches his tool be kicked over his head by a whirling menace. Fundamentals are necessary to learn and practice. The old adage of "walk before you run" works well here.
Wood turnings all work alike; prepare, turn, sand, and finish. The preparation may range easily from chainsaw and log to band saw and board or drill press and pen blank, but wood must be prepared to go on the lathe. Segmented turners will cut and glue for ages but it is all to prepare the wood to go on the lathe.
Turning may be for spindle or faceplate work but tools are still needed to be sharp and presentation needs to be clear. Different woods cut a little differently and need to be learned and approached in their own manner. Too many a new turner has been discouraged with the common spruce or pine of the flat worker to later be amazed at the nice cutting qualities of a piece of maple or ash. Each style of tool requires a slightly or greatly differing approach, but they are all able to be learned and familiarity with one makes the next easier.
Sanding is as important to the wood turner as to any other wood worker. The person who looks at the final piece looks at the surface, not the work in it. Finishing can be as elaborate or as simple as one likes, providing it fits the piece. Some call for dyes, painting, carving, piercing, pyrography or a combination of these and other embellishments. For others it would be gilding the lily.
The fundamentals well learned will let us approach that beautiful piece of hideously rare and possibly expensive wood with confidence. Learning is good.